This case is the equipment configuration plan for a 1600-ton limestone production line in Zhejiang. After the project is completed, it can be radiated to many surrounding counties and cities. It has unique geographical advantages and can provide high-quality and sufficient building sandstone aggregates for this area and surrounding areas. It will greatly promote the rapid development of infrastructure projects in the region, and at the same time provide demonstration effects for the construction of green mines and smart mines.
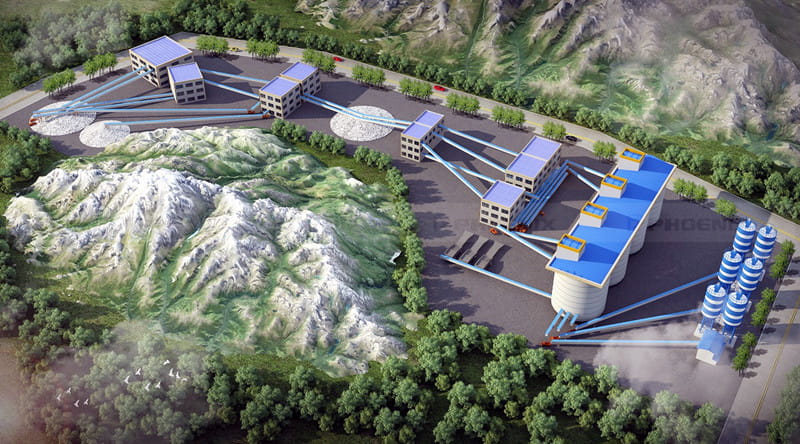
1. Overview of limestone production line:
1. Design capacity: 1600t/h
2. Design concept and program advantages: This program combines high efficiency, energy saving, environmental protection, safety and other core concepts, combined with the local sand and gravel market demand, raw materials and customers' requirements for high-quality concrete, in order to meet the major material customer groups ( Concrete mixing station, asphalt mixing station, dry mixing mortar station, civil materials, water stabilizing mixing station, etc.) Material characteristics of the configuration plan.
The crushing and screening line is designed with double production lines, and the single-line production capacity can reach more than 800 tons per hour. The advantage of the double production line over the single production line is that the production capacity is guaranteed and the production cost is relatively low. The double production line can adjust the production equipment according to the market sales situation. Cost control when reaching high and low peak materials.
2. Introduction of the technological process plan of the limestone production line:
1. Brief introduction of technological process:
This limestone crushing production line was independently designed by Shanghai Hengyuan Road and Bridge Group Co., Ltd., in order: two E-PV912, four CF400 counter-attacks, three HB-1000 vertical shafts, and one VISI1000 vertical shaft. The transfer piles are designed between the three-stage crushers, which can realize the independent operation of the three-stage crushers. When a certain crushing equipment is overhauled and maintained, other crushing equipment can continue to operate, thereby improving the operating time and efficiency of the equipment. At the same time, it can reconcile the production capacity differences of all levels of crushing equipment, maximize the operation of all levels of crushing equipment at full load, minimize energy consumption, and create energy-saving mines.
Two B1400 belt conveyors are used to transport the two heads to break the PV912 to the intermediate pile, and then two B1400 belt conveyors are used to transport four two-breaker counter-strikes to break the CF400. , 0-3mm sand goes directly to the finished material pile, 3-40mm stone material enters the next transfer material pile, and stone material larger than 40mm returns to the first transfer material pile. The second transfer pile is transported to three vertical shafts to break HB1000 through two B1400 belt conveyors, and its output is transported to four 4YK3072 screening finished products 0-5mm, 10-20mm, 20-28mm through two B1200 belt conveyors. The mixture of 5-10mm and 28-40mm is transported to a vertical shaft to impact and break the VSI1000 before being crushed.
The output of the fourth vertical shaft breaking VSI1000 is transported to two 4YK3072 circular vibrating screens through a B1200 to screen the finished products 0-5mm, 10-20mm, 20-28mm. The mixture of 5-10mm and 28-40mm also returns to the vertical shaft to break the VSI1000 and continue to break. All the finished 0-5mm sand can be washed and dewatered by three sets of sand washing machine 2XL-1115 and dewatering screen TSS2460 to obtain high-quality machine sand. When 5-10mm of product aggregate is needed, the aggregate can be transferred to the finished product silo through the switching of the hopper.
2. Sand and aggregate control:
1. Aggregate shaping: use vertical shaft to shape the aggregate.
2. 0-5mm mechanism sand desilting: on-site design reserves equipment positions such as sand washer, dewatering screen, etc. According to the gradation of the finished product produced, it can choose to use powder selection, water washing, powder addition and other process methods for control level Match.
3. Brief introduction of crushing and screening equipment configuration and production capacity of each workshop:
All device configurations are shown in Figure 1, Figure 2, Figure 3, Figure 4 and Figure 5 below
The equipment configuration is not listed, please consult the sales staff of Shanghai Hengyuan Road and Bridge Group Co., Ltd. to get the latest equipment list.
4. Project advantages:
1. In response to the country's promotion of green mine construction, this production line adopts a workshop-style design, which is a primary crushing workshop, a semi-finished product silo workshop, a medium crushing workshop, a fine crushing workshop, a screening workshop, a finished product silo workshop, and belt conveyors between workshops. The machine is connected in a suspended manner, the belt conveyor and the maintenance walkway are fully enclosed, the road in the factory is hardened, and the road is greened on both sides.
2. Environmental protection: A bag-type dust collector is used in the workshop to suppress dust, and a water spray system is arranged on the top of the workshop to cooperate with the dust removal equipment to reduce dust, so that the dust emission in the production process of the entire production line is within the scope of environmental protection requirements.
3. Safety: Separate the strong and weak electricity to separate the power distribution room and the control room, keep the operator away from the high-voltage power supply, and minimize the safety accidents of electricity consumption.
4. Overhaul: Each equipment workshop is equipped with simple driving, which is convenient, fast and safe when overhauling equipment.
5. An electric valve is installed under the finished product silo, and a belt conveyor is arranged at the lower part to transport the finished products of various specifications to the silo of each mixing station through a belt conveyor, which reduces the environmental pollution and cost caused by the loader and the use of the loader, and realizes the mixing station Process control.
6. Automated loading system: A belt conveyor is designed under the four finished product silos, which can transport quantitative aggregates of various specifications to the automatic loading system to realize dust-free automatic loading.
7. Energy saving:
① Multiple visual high-definition cameras are used in the production process to achieve unmanned production in the production line, reducing the number of workers to reduce potential safety hazards and reduce production costs.
② Shanghai Hengyuan's supporting electrical control equipment is a patented product, which can realize a 1000KVA transformer load and a 2000KW load (and so on), reducing the installed capacity of the transformer, thereby reducing the transformer installation fee, purchase fee, high-voltage cable purchase fee and installation fee, saving transformer Landline charges. The total installed capacity of this production line is about 6000KW, and the 7500KVA transformer needs to be installed according to the conventional requirements to meet the 6000KW power demand. If this patented product is used, only 3000KVA transformer can meet the on-site 6000KW power demand, saving 4500KVA transformer, saving monthly The transformer landline fee is: 4500*26 yuan/KVA=117000 yuan, and the annual savings: 117000*12=1404000 yuan.
③Using the patented reactive power compensation system, the power factor is guaranteed to be above 0.95, so as to achieve energy saving, which is more than 15% energy saving compared to conventional control systems.
5. The quality and control method of the finished products of sand and gravel aggregates:
1. Mud content control: After secondary crushing, that is, after impact crushing, use a vibrating screen to sieve out 0-3mm sand. If there is much mud in the raw material, in this screening step, the mud in the raw material will be sieved out completely to ensure that the subsequent products will no longer contain mud.
2. Aggregate particle size control: The system uses counterattack as second-level crushing. Its particle size and sand yield rate are both better and higher than cone crusher. In order to further obtain a better output particle shape and improve the sand production rate, the three-stage crushing uses a vertical shaft crusher, and obtains the finished product after screening.
3. Machine-made sand crushing: After a certain amount of machine-made sand is obtained in both the second-stage counter-attack breaking and the third-stage vertical shaft breaking, in order to obtain a higher ratio of machine-made sand, the sieved 5-10, >28mm stone material is transported to the vertical shaft Type sand making machine to make sand, so as to obtain a mechanism sand rate of nearly 60% overall.
4. Consolidation control: on-site design reserves equipment positions such as sand washing machine, dewatering screen, powder separator, and pulverizer. According to the gradation of the finished product, we can choose to use powder selection, water washing, powder addition and other process methods. Perform control grading.
6. Self-recommendation from the equipment provider of limestone crushing and screening production line:
On the basis of conscientiously summing up and drawing on the design of complete sets of high-quality crushing and screening programs at home and abroad, Shanghai Hengyuan Road and Bridge Group Co., Ltd., plus more than 20 years of extensive experience in the sand and stone crushing industry, have studied and analyzed various types of stone materials in detail Characteristics, combined with the performance characteristics of the equipment, after years of unremitting efforts, a complete system design theory for complete crushing and screening equipment has been formed, and it has the production capacity to design and manufacture single-line crushing and screening equipment under 3000t/h; Over the years of continuous development and growth, its registered trademarks are "Shan Sui" and "Phoenix" brand series crusher equipment, which has been recognized and accepted by many customers at home and abroad, and many first-line projects have become local model projects. Welcome customers at home and abroad to come to consult, we will treat each customer with better product quality and perfect after-sales service.
The above is the detailed configuration plan and process plan design of the 1600-ton limestone production line. If you need to know the total price of the production line, you can call our service hotline to get it, or leave a message on the website for consultation, thank you for your attention!